Valkyrie Factory Tour 2024

Valkrie Tour:
This article is being updated in real-time over the next few days, so while we continue to take pictures, film some videos, and ask their team lots of question, please enjoy the gallery below. Remember to stay tuned, as over the coming two weeks we’ll be covering a lot more, and visiting Computex 2024 to see all the latest product launches!

Here we are on our fantastic tour of China, with our first stop at the Valkyrie factory and HQ to check out the latest products, but also get an exclusive behind the scenes look at how their products are created. Most people have little to no idea what goes into a products development, and we’re looking forward to pulling back the curtain.
New Product Teasers
While we’ll be seeing these in a more glorious presentation at Computex 2024 next week, we got a sneak peak at some new and improved products for 2024 and beyond. Such as their new AIO designs, fans and air coolers.

They’ve made some unique improvements to the pump design with customisation options and magnetic mounts to give users more flexibility.

You can easily add custom graphics and decals to the block to suit your style, and I love that see-through design!

New and improved daisy chain cable designs on their new AIO.

And a 3-pin wireless connection for the block topper, which supports all four orientations.

Their new affordable tower air cooler, with a clean and simple slim design, it’s sure to appeal to budget system builders.

However, it still packs some premium aesthetics with its futuristic top panel and display.

Now, let’s get out of the air conditioned meeting room, there’s a hot and sweaty factory to explore!
The Factory Tour Begins

The factory is pretty hot and noisy, which you’re sure to hear in our upcoming video. However, it was a fun tour. Starting with the ground floor, where fresh materials are imported in the front of the factory and go straight into various presses.

There are tooling racks off to one side, it makes sense to keep these on the ground floor as they’re extremely heavy, and designed to go into the also extremely vast and heavy presses.

As you can see, products can be fed into the machine that moves up and down and applies many tonnes of force, to shape or cut metal to the appropriate specifications.

This machine stamps out fins that can later be formed into heatsinks, and here you can see new tooling being inserted, being changed for each component and product run.

The next machine is drum fed aluminium, which is them stamped into smaller components such as CPU socket brackets.

The clock on the right shows it’s pressing 64 of these every minute.

Everything from the brackets, the washers, the plates and more are made in house, rather than buying little components elsewhere, giving them control over the materials and quality, but also ensuring they can keep costs down and get things done much faster as parts are needed for assembly.

And they stamp out crates upon crates, thousands of tiny parts, stacked and ready to go to the next floor.

Some of the Intel/AMD are quite technical, so they’re hand fed into the machine rather than automated, being placed on small shaping blocks then stamped to add text, holes, and give them their overall finished design.

As you can imagine, they get through rather a lot of them, with around 30 boxes already stamped out by mid-day, but this is a part that could be used on multiple product designs.

As orders come in, they can build these parts quickly, and ensure the product assembly lines get the parts they need for each product run.

With each component requiring different tooling, there is understandably a lot of tooling here, with row upon row, and each one is so heavy it takes a forklike, pallet lifter or multiple people to move just one.

There also appears to be some workshop space for in-house modification and maintenance of these blocks.

Moving onto the production assembly, there are rows of conveyer belts that move slowly, with each station having a worker taking from their box of the chosen component and adding it to the product.

Some products require additional tooling work, such as drilling holes, polishing and other modification.

Here we saw them assembling huge copper heatsinks that they designed for industrial lighting products.

Here other products such as heatsinks for air cooling are beginning to take shape. It’s interesting to see it’s so hands on too, with people inspecting the work at each station to ensure the quality is at its best.

Here they’re applying liquid solder to the heatpipes.

The products then go through an absolutely massive oven, which heats the solder ensuring everything fuses by the time it passes out the end, and yes, it’s pretty damn toasty to be near this in an already hot country.

There are workstations to deal with fitting smaller screws and other more precise soldering jobs.

It’s a surprisingly complex operation too, you think it’s all just done by machines, but the care and attention required to assemble these products was a surprise, and the human element is a big factor here.

Had to snap this one, we had permission of course, but it made some of the staff who look at us in surprise… ha!

As products work their way down the line, they end up at packing stages, ready to be made into complete products for consumers.

Such as these cables, and yes, there are a lot!

And as you might expect, there are vast amounts of orders building up at the top floor of the factory, ready to be shipped out. Materials in the bottom floor, working up to secondary tooling, assembly, packing, and then they’re craned out the top of the building and into trucks to be send around the world.

Image Gallery

Want to keep up with the latest news from eTeknix @ Computex 2024? Follow us on Facebook, Twitter/X, TikTok, Discord, and for the best video coverage of the show, check out the eTeknix YouTube!
Thanks to all of our sponsors for making our Computex 2024 coverage possible!
Antec – be quiet! – BiWin – Colorful – DeepCool – Endorfy – FSP – ID-Cooling – INNO3D – KLEVV – MSI – NZXT – PGW – PALIT – Sapphire – Sharkoon – TEAMGroup – Thermal Grizzly – Thermaltake – Valkyrie – XPG
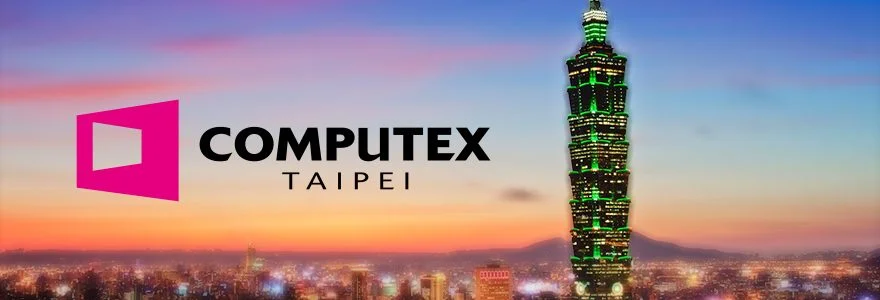